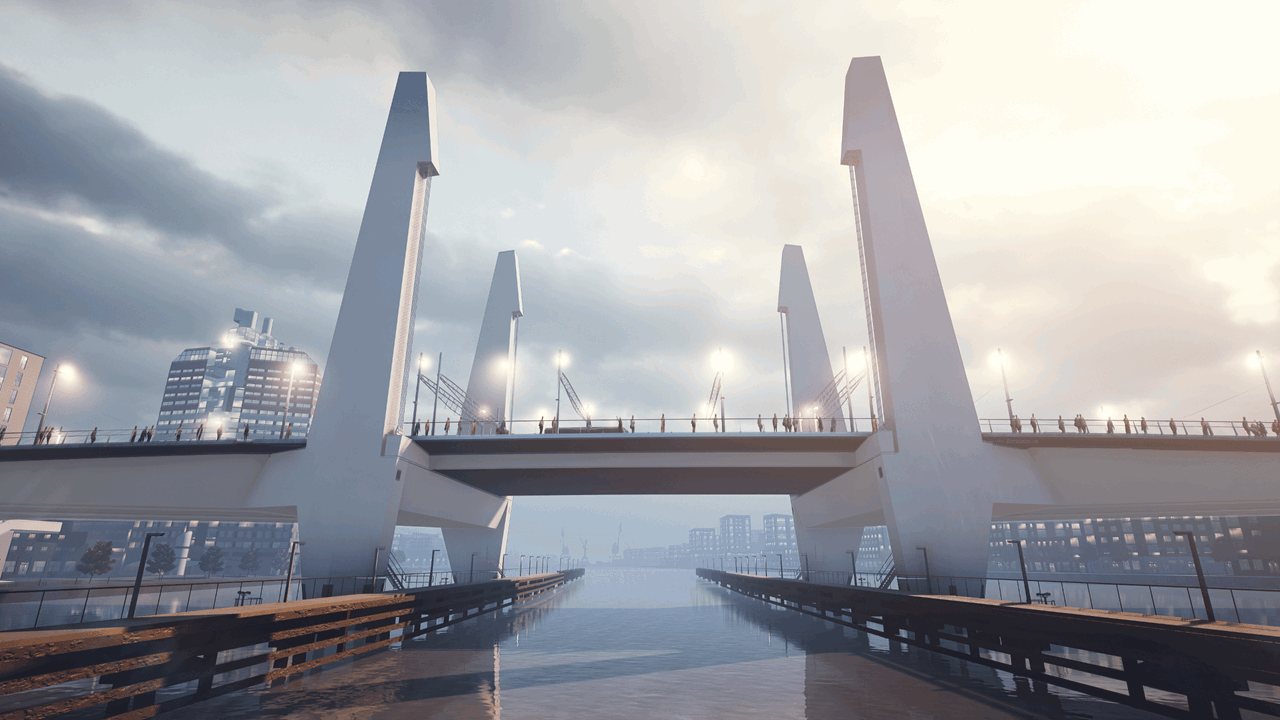
Expander System pivot pins perfect for complex bridge design
Custom Expander axles are used to secure critical pivot joints on the vertical-lift Hisings Bridge, Gothenburg. Here, precision and reliability are crucial to a mechanical system that raises and lowers an 800-ton central lift span, allowing ships to pass and transport crossings to perfectly re-align. Expander provides a permanent solution to lug wear when handling these dynamic loads.
In May 2021, the Hisings Bridge (Hisingsbron) in Gothenburg, Sweden, opened to transport across the Göta Älv river. First out were cars, buses, bicycles and pedestrians. The trams rails were finished during the summer.
Commissioned by the Traffic and Public Transport Authority of Gothenburg, the project design started in 2009 and construction in 2016. Reliability and the use of proven technology were vital requirements in their specification for the lift span and its machinery. A joint venture between Skanska and MT Højgaard won the tender and ran the project.
In a 2013 design competition, there were suggestions for different types of movable bridges: bascule bridges, swing bridges and vertical-lift bridges. The winner was a vertical-lift bridge, Arpeggio, designed by a consortium of architectural firms and project designers. The jury’s decision focused on viability, development and functionality.
The bridge will be a symbol of Gothenburg, a landmark associated with the city, in harmony with its character and landscape. The Arpeggio design is solid, with strong dimensions and a proven technical solution. The open water under the bridge, which will contribute to a vibrant environment of urban sports and boating, was also a positive factor.
Many suggestions before finding the right one
The Hisings Bridge is a 440-meter long vertical-lift bridge where a central lift span, supported by four steel towers (pylons), is raised to 28 meters when a ship needs to pass. After each lift, the lift span must return to the 12-meter level with exact precision so that the lift span tram tracks align perfectly with those on the roadway.
Construction engineers ELU designed the steel pylons and the roadway. They commissioned Tikab Strukturmekanik AB to develop the lift span machinery. Peter Lassfolk, Mechanical Design Engineer and Network Administrator at Tikab, designed the machinery together with his team.
Lassfolk says that the Hisings Bridge was one of his most demanding assignments: “The biggest challenge was to develop machinery that could fit the limited space. It was complicated, and we scrutinized quite a few different solutions before deciding on the current one.”
Complex system for the lift span
It is vital that the 37-meter-wide lift span, which weighs 800 tons, can be raised and lowered quickly. It is fixed to 16 cables, four in each corner. The cables go up to cable wheels at the top of the pylons, then down to a counterweight. Four thinner cables connect to machinery that pulls the counterweight.
When the lift span is raised, it is actually the counterweight that is pulled down. When the lift span is lowered, the lifting force is removed so that the lift span's weight makes it stay down. In each pylon, there are two large hooks that, through a jack, pull down the lift span, removing the lifting forces. The Expander System is attached to the hooks.
Tikab oversaw the design, and SH Group manufactured and tested the machinery. Tikab suggested the use of Expander System, and SH Group agreed that this was the best solution. Expander System is a solution to lug wear consisting of three main parts: a pin in the middle and two expansion sleeves, which are installed directly in the existing mounting. When you tighten fasteners from the sides, the expansion sleeves are pressed up the tapered ends of the pin, expanding and conforming to the mounting.
Reliability and long service life
“We’re using an extra-large, tailor-made Expander axle,” Lassfolk explains. “The main advantage is how they facilitated the assembly. We needed to install big components into a rather narrow space but using Expander System was a smooth process.”
Using Expander System also increases service life while minimizing maintenance. Usually, axle movement causes lug wear, which over time makes the holes oval and increases the play.
“If you use Expander System, you remove that play,” says Brian Troest, Country Manager Denmark and Sweden, Nord-Lock Group. “The pin must be smaller than the hole to pass through it. However, Expander System adjusts the difference between the hole diameter and the expansion sleeve pin diameter at the end of the Expander pin.”
Outlasting other alternatives
When you tighten the bolt or nut on the side, the expansion sleeve is pushed into the hole, where it expands with an outer cone on the shaft and an inner cone in the sleeve. “Then you get a product that doesn’t cause any problems and which will outlast any alternative solution,” says Troest.
Over the years, Lassfolk has used Expander System in several designs. “It was natural to choose this solution for the Hisings Bridge project. You obviously want to use high-quality products,” he concludes.
This article is taken from Nord-Lock Group’s whitepaper Bridge Design, Construction & Maintenance: Insights and Best Practices for a Rapidly Changing Sector (2021). Click here to read and download the 70-page white paper
The Hisings Bridge (Hisingsbron), Gothenburg
Inaugurated: 2021
Total length: 440 meters
End-customer: City of Gothenburg
Design: TIKAB
Nord-Lock Group solution: Expander System
Benefits: Easy assembly, increased service life and minimal maintenance