
Installation Instructions
Stepped Pin, Spanner Nut Secured
5.4

Following these instructions will ensure that the Expander System is installed correctly and the pivot life is prolonged.
Congratulations! You have purchased a custom engineered solution to the pivot wear problem on your machine. Contact your dealer or Expander before proceeding if you have any questions.
Expander System pivot pin comes with a warranty against lug wear of 10 years / 10 000 hours in operation (whichever comes first) from the date of purchase.
The picture shows a female axle, but the principle is the same for other designs.

1 Bolt. 2 Washer. 3 Sleeve. 4 Axle (Pin). 5 Securing spanner nut. 6 Threaded washer.
Preparation
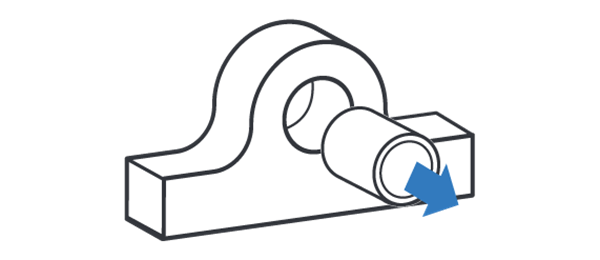
Remove any bushings in the lugears to eliminate future wear between the bushing and the mounting lug.
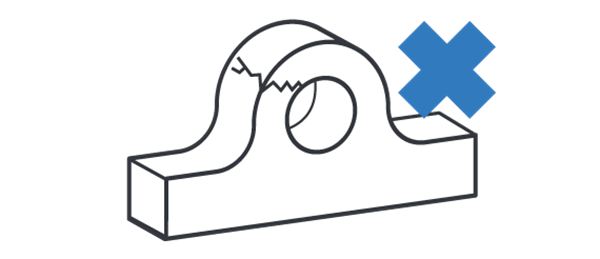
Repair any structural damage i.e. cracks or bent lug ears before installation.

Smooth out any irregularities in the bore surfaces.

The difference between min and max diameter in the worn lugs must be within .06” (1.5 mm) for the sleeves to fit correctly.
ATTENTION! If the worn lugs diameter at any point is 2 mm (.080”) or more over original lug diameter contact your dealer or Expander System. You will need oversized sleeves.
Installation
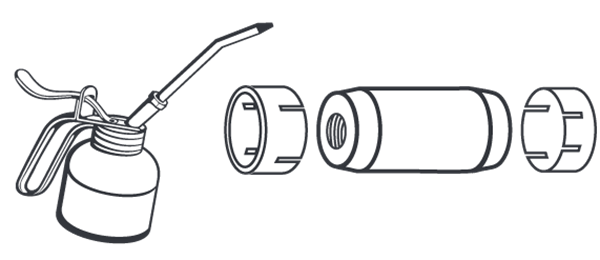
Grease the sleeves and axle with grease available, preferably graphite grease. Do not grease the threads!

NOTE! If applicable: position greasing outlet 90 degrees to force direction to minimize stress concentration at outlet.

The spacer is always positioned on the opposite side of the stepped part of the axle. If the pivot already has a spacer, leave it in its position. If the Expander System includes a spacer, place it between the inner sphere of the bearing and the lug ear, with the bevel facing the bearing.

Insert the axle. Install securing spanner nut and threaded washer on the side with small axle diameter. Position to achieve a gap between the threaded washer and the lug. Mount and tighten the fastener until the axial play is eliminated.

Install sleeve, washer and fastener on the side with large axle diameter. Tighten the fastener with recommended torque.

Remove securing spanner nut and threaded washer. Install sleeve. Reinstall securing spanner nut, threaded washer and fastener. Keep the securing spanner nut loose and tighten the fastener with recommended torque. Finally tighten the securing spanner nut against the lug.
Torque recommendations

Hex Bolts
Torques M12-M24 ± 10%, M30... +30/-0%
M12 | M14 | M16 | M20 | M24 | M30 | M36 | M42 | |
Nm | 70 | 115 | 175 | 350 | 500 | 600 | 700 | 900 |
lb-ft | 52 | 85 | 129 | 258 | 369 | 443 | 516 | 664 |

Hex Nuts: Standard Height
Torques M12-M24 ± 10%, M30... +30/-0%
M12 | M14 | M16 | M20 | M24 | M30 | M36 | M42 | |
Nm | 65 | 115 | 175 | 250 | 350 | 500 | 600 | 700 |
lb-ft | 48 | 85 | 129 | 184 | 258 | 369 | 443 | 516 |

Hex Nuts: Low Height
All Torques ± 10%
M12 | - | M16 | M20 | M24 | M30 | - | - | |
Nm | 60 | - | 125 | 200 | 275 | 350 | - | - |
lb-ft | 44 | - | 92 | 148 | 203 | 258 | - | - |

Spanner Nuts
All Torques ± 10%
M17 | M25 | M35 | M45 | M55 | M65 | M75 | M85 | |
Nm | 50 | 120 | 250 | 500 | 600 | 700 | 800 | 900 |
lb-ft | 37 | 89 | 184 | 369 | 443 | 516 | 590 | 664 |

Securing Spanner Nut
Max Torque
....M100 | M100.... | - | - | - | - | - | - | |
Nm | 50 | 80 | - | - | - | - | - | - |
lb-ft | 37 | 59 | - | - | - | - | - | - |
Final Check

After initial torque, grease the pivot (if applicable), move the machine through full range of motion several times and recheck the torque. Check the torque after 10 hours, 40 hours and at regular service intervals to ensure proper seating of the sleeves.

Ensure that there is a minimum distance of 0,5 mm (0.02”) between the washer and the lug. NOTE! If flange design for easy removal of the sleeve is used there should be a minimum distance of 6 mm. ATTENTION! If the washer is in contact with the lug, contact your dealer or Expander System.