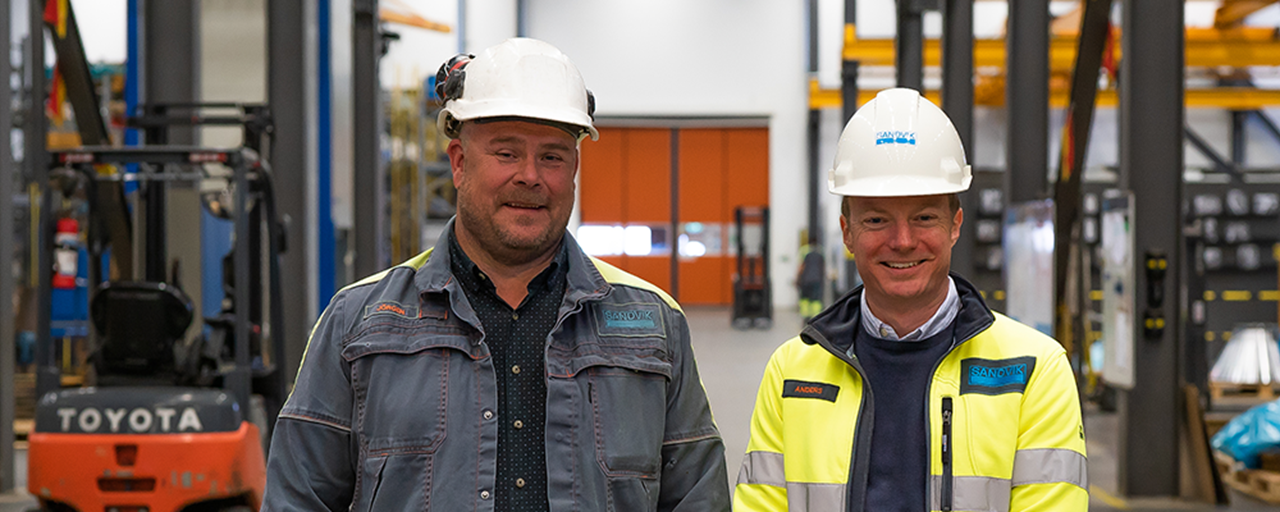
Der Kreislauf: Bergbaumaschinen und Manganstahl
Sandvik Rock Processing Solutions liefert nachhaltige Produkte für die Bergbauindustrie. Das Team im schwedischen Svedala stellt hochwertige Kegelbrecher her, bei denen die Verschleißteile aus Stahl kreisförmig sind. Durch die Verwendung von mehr als 90 % recyceltem Rohmaterial ist das Unternehmen zu einer der nachhaltigsten Mangangießereien der Welt geworden. Wir sprachen mit Anders Åkesson und Jörgen Petersson, den Gewinnern des Sandvik Sustainability Award, um herauszufinden, wie.
Kegelbrecher für die Gesteinsaufbereitung sind um eine Kammer herum gebaut, die aus einem inneren und einem äußeren Mantel besteht. Der innere Mantel bewegt sich zur Seite, und die Steine fallen dazwischen und werden zerkleinert. Im Bergbau werden sie eingesetzt, um Mineralien aus Erzen zu gewinnen. Im Baugewerbe verarbeiten sie Gestein zu Asphalt, zum Beispiel für den Straßenbau.
Obwohl die meisten Brecherhersteller einen gewissen Prozentsatz an recyceltem Schrott verwenden, hat Sandvik durch ein ehrgeiziges Rückkaufprogramm, Investitionen in Anlagen und das Umschmelzen alter Teile, um recyceltes Metall in seine neuen Brecher einzubauen, einen bemerkenswerten Kreislaufanteil von 92 % erreicht.
"Ferromangan-Stahl hat einen recht hohen CO2-Fußabdruck. Durch die Einführung eines Rückkaufprogramms wird der Bedarf an diesem neuen Material verringert, was einen großen Einfluss auf die Treibhausgasemissionen hat. Durch die Rückkäufe sparen wir jedes Jahr rund 16.000 Tonnen CO2 ein", sagt Anders.
Brecher sind große, schwere Geräte - wie funktioniert der Rückkauf in der Praxis?
Für geografisch nahe gelegene Kunden betreibt Sandvik ein Austauschprogramm und es ist möglich, Güterzüge für den Transport der Metallgeräte und -teile zu nutzen. Nähe und Volumen sind die Schlüsselfaktoren. Dies ist machbar, da Sandvik einen großen europäischen Markt hat, in dem die wichtigsten Gießereien ansässig sind.
Für die Kunden gibt es Anreize am Rückkaufprogramm für Verschleißteile teilzunehmen, wodurch sie bis zu 40 % bei diesen "wiedergeborenen" Lösungen sparen können.
"Es ist ein bisschen wie das Rückerstattungssystem, das für das Recycling von Aluminiumdosen in Supermärkten verwendet wird, nur in größerem Maßstab. In Bergwerken und Steinbrüchen kann es vorkommen, dass die verschlissenen Teile vorher liegen geblieben sind, so dass es für den Kunden sinnvoll ist, etwas Geld zu sparen, indem er seinen Schrott bei uns recycelt", erklärt Jörgen.
Bei großen Entfernungen, bei denen der Rücktransport der Teile einen zu großen CO2-Fußabdruck hinterlassen würde, arbeitet Sandvik stattdessen eng mit Schrotthändlern zusammen, die sich auf ihre Manganstahlsorten spezialisiert haben. Die Schrottpreise können hoch sein, so dass es sowohl wirtschaftlich als auch ökologisch vorteilhaft ist, verschlissene Teile direkt zurückzuholen und den Stahl für den Guss neuer Modelle wieder einzuschmelzen.
Generell könnten die Kunden die Zuverlässigkeit der recycelten Produkte in Frage stellen. Vor allem die Stahlmischungen müssen zu 100 % genau sein, wie kann man also die Qualität garantieren?
Das Team von Anders hat in die Ausrüstung investiert, um die Chargenmischungen zu kontrollieren. Geräte wie tragbare Spektrometer werden eingesetzt, um die Stahlsorten zu identifizieren und die vier wichtigsten Legierungszusammensetzungen der Gießerei auf dem Schrottplatz zu klassifizieren, damit die Qualität der Eingangsmaterialien gewährleistet ist. Der Vorteil eines gut eingeführten Recyclingprogramms ist, dass der Schrott oft schon gut sortiert und genau klassifiziert ist, so dass Jörgens Team die Legierungen nur selten korrigieren muss.
Der Stahlschrott wird dann im Ofen umgeschmolzen, wobei die Proben durch das Spektrometer geschickt werden, um den Kohlenstoffanteil und die Legierungszusammensetzung zu überprüfen. Die neue Mischung kann dann spezifischen Produktrezepturen zugefügt werden und zwar mit einem Kontrollniveau, das eine gleichbleibend hohe Qualität der neuen Schmelzen gewährleistet.
Wo liegt die größte Herausforderung? Die Gestaltung einer Kreislaufwirtschaft, die Implementierung der Infrastruktur oder die Einbeziehung der Kunden?
In der Vergangenheit hat Anders hart daran gearbeitet, den Business Case bei den Kunden aufzubauen, aber jetzt erlebt er ein eher organisches Interesse von deren Seite, da die Kunden aktiv nach nachhaltigeren Lösungen suchen.
"Die großen Bergbauunternehmen suchen nach Möglichkeiten, ihren Fußabdruck zu verringern und ihre eigenen Nachhaltigkeitsziele zu erreichen", sagt er.
Was die Umsetzung der Kreislaufwirtschaft betrifft, so begann das Team mit einer "Cradle-to-Grave"-Analyse seiner Produkte. Anhand einer detaillierten Inspektion der Lieferkette, der Betriebsabläufe und der Logistik wird festgelegt, wie die Kreislaufwirtschaft gemessen werden soll und es wird ein Fahrplan für die Rückführung von Produkten erstellt, um den Kreislauf zu schließen.
Diese Lebenszyklusanalyse ist zeitaufwendig, aber sie bildet auch die Grundlage für die Umweltproduktdeklaration (EPD) von Sandvik. In diesem Dokument werden die Umweltauswirkungen eines Produkts in Bezug auf Emissionen, Energieverbrauch und ähnliche Kriterien erfasst. Das Ergebnis ist ein Dokument, das die Nachhaltigkeit der Mangan-Brecher-Verschleißteile von Sandvik im Vergleich zu alternativen Anbietern belegt.
"Eine EPD bietet einen Wettbewerbsvorteil. Wir sind vielleicht nicht die billigsten auf dem Markt, aber wir beweisen, dass wir einen geringen Fußabdruck hinterlassen", betont Anders. "Das ist etwas, das die Kunden allmählich als Deal-Breaker sehen und das dafür bürgt, dass die Industrie in Zukunft Verantwortung für die Nachhaltigkeit übernimmt", fährt er fort.
Der lange Weg zur Kreislaufwirtschaft
Die Umstellung der Produktionsprozesse und Geschäftsmodelle eines globalen Unternehmens braucht natürlich Zeit. Angesichts der Komplexität werden Gewinne, je weiter man geht, auch immer marginaler und teurer. Anders' Team hat vor einigen Jahren einen hohen Kreislaufanteil (80 %) erreicht, konnte aber in den letzten fünf oder sechs Jahren ein Niveau von 92 % erreichen.
Die Erstellung der EPD dauert Jahre, aber die aus einer umfassenden Lebenszyklusanalyse gewonnenen Erkenntnisse bieten eine viel bessere Kontrolle über die Verbesserung Ihrer Prozesse aus der CO2-Perspektive. Für Anders hat die Analyse speziell die Stahllegierungen identifiziert, die in Bezug auf die Emissionen am schlimmsten sind. "Von dort aus kann man ein Projekt starten, um diese Elemente durch eine nachhaltigere Rezeptur zu ersetzen", erklärt er.
Obwohl Sandviks Konzernziel von 90 % Kreislaufwirtschaft bis 2030 bereits weit übertroffen wurde, besteht ein Ziel darin, Wissen zu teilen und mit Zulieferern zusammenzuarbeiten. Anders hält es für möglich, das Rückkaufprogramm auf Gebiete auszudehnen, in denen eine große Anzahl von Sandvik-Brechern installiert ist, und eine effektive Zusammenarbeit zwischen diesen Kunden und den örtlichen Stahlgießereien aufzubauen.
"Es ist einfacher, wenn man seine eigene Gießerei hat, aber jetzt müssen wir uns auch auf unsere internationalen Zulieferer konzentrieren, um sie dazu zu bringen, ihre eigene Kreislaufwirtschaft zu verbessern."
Preisgekrönte Nachhaltigkeit
Trotz starker Konkurrenz aus anderen Geschäftsbereichen wurde die Arbeit mit Brecher-Verschleißteilen mit dem Sandvik-internen "Sustainability Award in Memory of Sigrid Göransson" ausgezeichnet. Die 1872 geborene Sigrid Göransson war die Enkelin des Sandvik-Gründers und sorgte dafür, dass sich das Unternehmen auf soziale Verantwortung und bessere Arbeitsbedingungen konzentrierte - zu einer Zeit, als dies noch selten war. Mit dem Preis werden die messbaren und nachhaltigen Auswirkungen von Anders und Jörgens Mission auf Wirtschaft und Umwelt gewürdigt.
Die beiden Kollegen verweisen auf die starke Forschungs- und Entwicklungsarbeit vor Ort und eine Unternehmenskultur, die den Fortschritt und die unermüdliche Teamarbeit fördert, die diese beeindruckenden Innovationen möglich gemacht haben.
"Wir sind stolz darauf, den Preis persönlich entgegenzunehmen, aber es hat mehrere Jahre und eine Teamleistung gebraucht, um diesen Punkt zu erreichen. Nachhaltigkeit ist Teil unserer täglichen Praxis geworden", sagt Jörgen.
Anders schließt: "Als größte Stahlgießerei Schwedens findet unsere Arbeit in der Branche Widerhall - die Reise ist also noch nicht zu Ende. Wir werden uns weiterhin auf den Lebenszyklus von Ersatzteilen und die Reduzierung von Abfällen konzentrieren und die Ziele von Sandviks 'Shift to Sustainability' anstreben. Ich bin sehr zuversichtlich, dass wir noch viel mehr erreichen werden".